Margate Dairy Bar & Burger – Margate City, New Jersey
Project Info
Client Margate Dairy Bar & Burger
Products Flood Log™
Location Margate City, New Jersey
Project Description
1800-square-foot property located two blocks from the Atlantic Ocean
Vulnerable to flooding from coastal storms and hurricanes
Renovation after Hurricane Sandy in 2012 added Flood Logs
Features easy deployment and storage, rugged construction that withstands corrosion
Clean, metal brackets blend in with the restaurant aesthetics
Just south of Atlantic City, the Margate Dairy Bar & Burger has been a favorite eatery for locals and visitors to the Jersey Shore since it opened in 1952. Just two blocks from the ocean and only three blocks from the bay, the Dairy Bar is vulnerable to coastal flooding from hurricanes and other Atlantic storms. In 2012, Hurricane Sandy destroyed most of the restaurant, including more than $100,000 in equipment. The event forced a major renovation of the Dairy Bar that included the installation of custom-built Flood Logs from Flood Panel to protect it from future storms.
Hurricane Sandy Forces Dramatic Renovation
The Dairy Bar has a long history in Margate City as the place for window service burgers and shakes. Named Best of Philly, Best of South Jersey, and Best Waffle in South Jersey for several years running, the iconic establishment draws thousands of visitors during a typical summer week and often attracts lines of customers that spill into the street.
Historically, the 1,800-square-foot property had been divided between the Dairy Bar and a connecting restaurant. Current owner Christopher Clayton purchased the landmark property in 2003, taking over the Dairy Bar and leasing out the adjoining space. In November 2012, Hurricane Sandy wiped out the restaurant’s four ice cream machines and other equipment valued at close to $100,000. “Being a small business owner in a seasonal town that deals with flood waters on the Jersey Shore is not for the faint of heart,” said Clayton.
Many businesses did not recover after Sandy, including the restaurant attached to the Dairy Bar. The vacancy gave Clayton an opportunity to begin a major, million-dollar expansion and renovation. He hired famed architect Richard Stokes to refashion the Dairy Bar in the Googie style, a modern form of architecture popular in the ‘50s and ‘60s that was heavily influenced by car culture, jets and the Space Age (think “The Jetsons”). The renovation increased the footprint of the original Dairy Bar and added new service windows, an outdoor dining area, and a new building with bathrooms, a prep area, new walk ins, second-floor offices, storage, and space for trash and recycling.
To qualify for flood insurance, the new Dairy Bar had to meet building codes from the Federal Emergency Management Association for structures in flood zones. The restaurant had three options: elevate, install flood vents, or dry flood proof. Elevation was not an option, since ramps from the window service area to the street would be required to comply with disability requirements. Flood vents were also out, since they allow water to flow through a building during a flood event and would expose equipment to flood damage. Dry flood proofing was the only option that would protect the restaurant’s assets and could withstand the hydrostatic pressure of flood waters and debris on the building.
Flood Panel Builds a Custom Solution for the Dairy Bar
The Dairy Bar’s general contractor Tortorice Construction considered several flood solutions and recommended Flood Panel’s Flood Logs to the architect. They contacted Bill Coleman of Flood Protection NJ, Inc., based in Northern New Jersey and a certified dealer for Flood Panel LLC. Together they designed and built a custom solution to match the Dairy Bar’s unique architectural requirements. “Flood Logs seemed to be the most economical and most feasible, so my architect and builder decided that was the route to go,” said Clayton.
When installed, the Flood Logs will add several feet of flood protection to the current elevation of the Dairy Bar property, a few inches higher than the flood level reached during Hurricane Sandy. Flood Panel prepared all the documentation required by FEMA to detail exact specifications, installation instructions, product testing, maintenance and emergency management plans. According to Clayton, “We weren’t buying flood protection as much as we were buying flood insurance protection.”
Clayton was very impressed with the expertise that Coleman and Flood Panel brought to the process. “If you’re going to flood proof your building or do any type of construction, you need to bring in people that are subject matter experts and can back up their work.”
Clayton’s favorite features of the Flood Logs are ease of deployment, easy storage and rugged construction. On a practice run, he and an employee were able to install the logs in less than two hours. Because the logs require minimal storage space, Clayton keeps them stacked onsite, so they can be deployed quickly. The logs are made of aluminum, which withstands rusting and the corrosion common in ocean communities. “It’s a good solution made for the shore that won’t get compromised because of saltwater, salt air or wind-blown sand,” said Clayton. “It’s a great long-term investment.”
In addition to practical features, the clean, metal brackets of the Flood Logs blend in with the geometric angles of the Googie style – an unexpected aesthetic benefit. “It has a rather unique application for my business because of the architecture outside. It’s almost like we put the brackets in as part of the design,” Clayton said.
Clayton is very confident in his Flood Panel investment. “When you get a nice rain coat and boots, you want it to rain. I hate to say it, but I wouldn’t mind getting a storm with a foot of water, just so I could deploy them and see them work. Bring it on!”
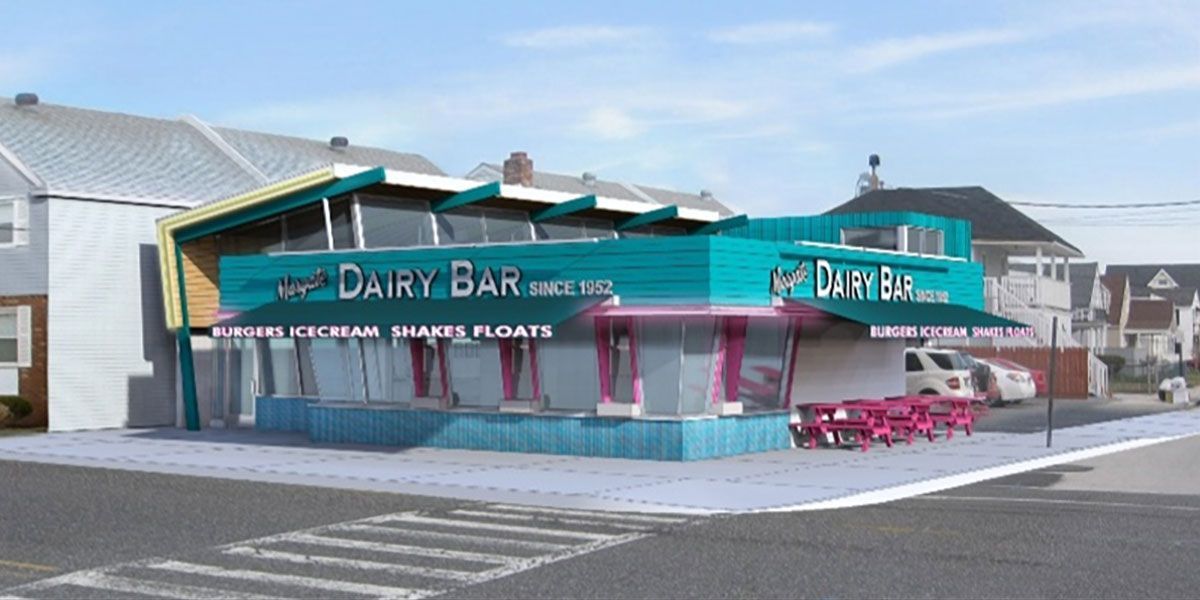
Project Info
Client Margate Dairy Bar & Burger
Products Flood Log™
Location Margate City, New Jersey
Project Description
1800-square-foot property located two blocks from the Atlantic Ocean
Vulnerable to flooding from coastal storms and hurricanes
Renovation after Hurricane Sandy in 2012 added Flood Logs
Features easy deployment and storage, rugged construction that withstands corrosion
Clean, metal brackets blend in with the restaurant aesthetics
Just south of Atlantic City, the Margate Dairy Bar & Burger has been a favorite eatery for locals and visitors to the Jersey Shore since it opened in 1952. Just two blocks from the ocean and only three blocks from the bay, the Dairy Bar is vulnerable to coastal flooding from hurricanes and other Atlantic storms. In 2012, Hurricane Sandy destroyed most of the restaurant, including more than $100,000 in equipment. The event forced a major renovation of the Dairy Bar that included the installation of custom-built Flood Logs from Flood Panel to protect it from future storms.
Hurricane Sandy Forces Dramatic Renovation
The Dairy Bar has a long history in Margate City as the place for window service burgers and shakes. Named Best of Philly, Best of South Jersey, and Best Waffle in South Jersey for several years running, the iconic establishment draws thousands of visitors during a typical summer week and often attracts lines of customers that spill into the street.
Historically, the 1,800-square-foot property had been divided between the Dairy Bar and a connecting restaurant. Current owner Christopher Clayton purchased the landmark property in 2003, taking over the Dairy Bar and leasing out the adjoining space. In November 2012, Hurricane Sandy wiped out the restaurant’s four ice cream machines and other equipment valued at close to $100,000. “Being a small business owner in a seasonal town that deals with flood waters on the Jersey Shore is not for the faint of heart,” said Clayton.
Many businesses did not recover after Sandy, including the restaurant attached to the Dairy Bar. The vacancy gave Clayton an opportunity to begin a major, million-dollar expansion and renovation. He hired famed architect Richard Stokes to refashion the Dairy Bar in the Googie style, a modern form of architecture popular in the ‘50s and ‘60s that was heavily influenced by car culture, jets and the Space Age (think “The Jetsons”). The renovation increased the footprint of the original Dairy Bar and added new service windows, an outdoor dining area, and a new building with bathrooms, a prep area, new walk ins, second-floor offices, storage, and space for trash and recycling.
To qualify for flood insurance, the new Dairy Bar had to meet building codes from the Federal Emergency Management Association for structures in flood zones. The restaurant had three options: elevate, install flood vents, or dry flood proof. Elevation was not an option, since ramps from the window service area to the street would be required to comply with disability requirements. Flood vents were also out, since they allow water to flow through a building during a flood event and would expose equipment to flood damage. Dry flood proofing was the only option that would protect the restaurant’s assets and could withstand the hydrostatic pressure of flood waters and debris on the building.
Flood Panel Builds a Custom Solution for the Dairy Bar
The Dairy Bar’s general contractor Tortorice Construction considered several flood solutions and recommended Flood Panel’s Flood Logs to the architect. They contacted Bill Coleman of Flood Protection NJ, Inc., based in Northern New Jersey and a certified dealer for Flood Panel LLC. Together they designed and built a custom solution to match the Dairy Bar’s unique architectural requirements. “Flood Logs seemed to be the most economical and most feasible, so my architect and builder decided that was the route to go,” said Clayton.
When installed, the Flood Logs will add several feet of flood protection to the current elevation of the Dairy Bar property, a few inches higher than the flood level reached during Hurricane Sandy. Flood Panel prepared all the documentation required by FEMA to detail exact specifications, installation instructions, product testing, maintenance and emergency management plans. According to Clayton, “We weren’t buying flood protection as much as we were buying flood insurance protection.”
Clayton was very impressed with the expertise that Coleman and Flood Panel brought to the process. “If you’re going to flood proof your building or do any type of construction, you need to bring in people that are subject matter experts and can back up their work.”
Clayton’s favorite features of the Flood Logs are ease of deployment, easy storage and rugged construction. On a practice run, he and an employee were able to install the logs in less than two hours. Because the logs require minimal storage space, Clayton keeps them stacked onsite, so they can be deployed quickly. The logs are made of aluminum, which withstands rusting and the corrosion common in ocean communities. “It’s a good solution made for the shore that won’t get compromised because of saltwater, salt air or wind-blown sand,” said Clayton. “It’s a great long-term investment.”
In addition to practical features, the clean, metal brackets of the Flood Logs blend in with the geometric angles of the Googie style – an unexpected aesthetic benefit. “It has a rather unique application for my business because of the architecture outside. It’s almost like we put the brackets in as part of the design,” Clayton said.
Clayton is very confident in his Flood Panel investment. “When you get a nice rain coat and boots, you want it to rain. I hate to say it, but I wouldn’t mind getting a storm with a foot of water, just so I could deploy them and see them work. Bring it on!”
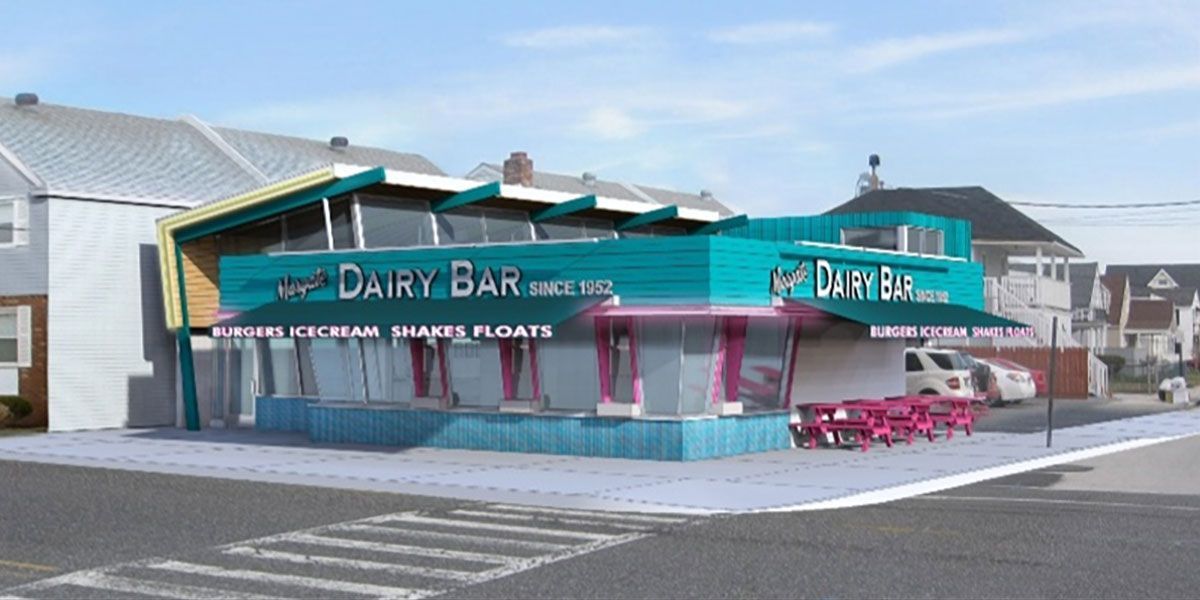